Hydroxyethyl cellulose (HEC) is a non-ionic, water-soluble polymer derived from cellulose, which is a natural polymer found in the cell walls of plants. Its versatility and functionality make it highly valuable in various industries, including pharmaceuticals, personal care, and construction. Understanding the intricacies of its manufacturing process can provide insights into its widespread utility and applications.
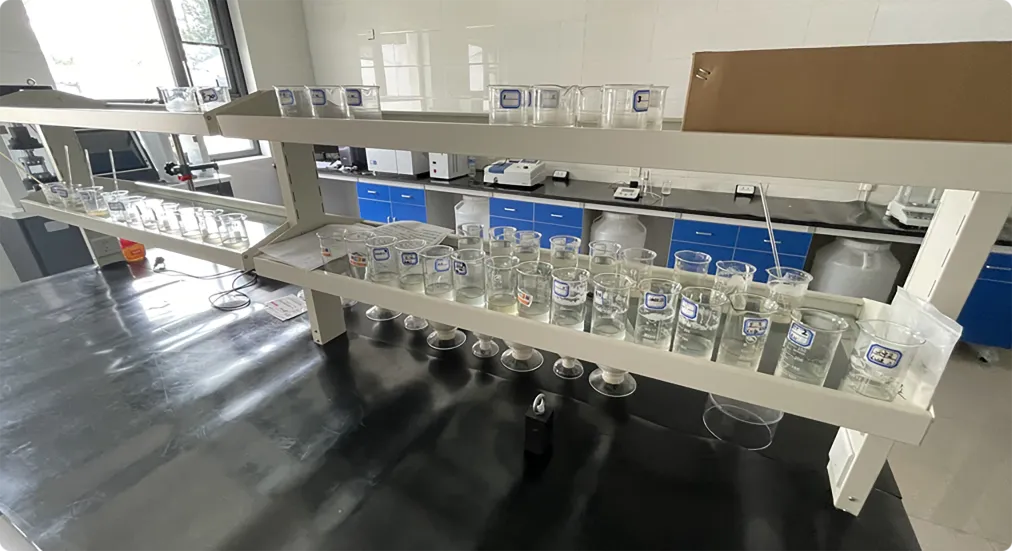
The production of hydroxyethyl cellulose starts with the selection of quality raw cellulose. This cellulose is typically sourced from wood pulp or cotton linters, both renowned for their abundance and purity. These materials are chosen because they provide a consistent starting base with the necessary structural characteristics. The cellulose is then cleaned and purified to remove any impurities that might affect the subsequent reactions.
The next crucial step in creating hydroxyethyl cellulose involves altering the natural cellulose structure through a process known as etherification. Here, the purified cellulose is reacted with sodium hydroxide (NaOH), transforming it into alkali cellulose. This conversion is critical as it activates the cellulose, making it more receptive to the modifications that will follow.
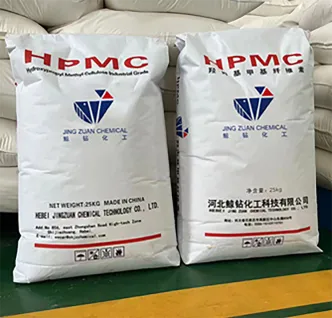
Etherification is further achieved by introducing ethylene oxide. The interaction between the alkali cellulose and ethylene oxide facilitates the attachment of hydroxyethyl groups to the cellulose backbone. This reaction is delicately balanced to ensure that the desired degree of substitution is achieved. The number of hydroxyethyl groups introduced determines the solubility, viscosity, and overall functionality of the final product. Controlling this degree of substitution allows manufacturers to tailor HEC for specific applications, from thickening agents in paints and adhesives to stabilizers in pharmaceutical formulations.
how is hydroxyethyl cellulose made
Post-reaction, the product undergoes several purification steps. The first involves neutralizing the reaction mixture to remove by-products and unreacted materials, ensuring that the final hydroxyethyl cellulose is of high purity. It is then thoroughly washed to eliminate residual salts and other impurities. This purification process is essential in achieving a product that is both effective and free from contaminants, contributing to its reliability and safety in sensitive applications such as pharmaceuticals.
The final stage before commercial distribution involves drying and milling. The filtered HEC is dried to achieve optimal moisture content, preventing microbial growth and prolonging shelf life. Once dried, the HEC is milled to a fine powder, enhancing its solubility and ease of use. The consistency in particle size distribution also affects its performance, necessitating precise control during this process.
Throughout the manufacturing process, quality control is paramount. Each batch of hydroxyethyl cellulose is subjected to rigorous testing to ensure that it meets the established industry standards. Parameters such as viscosity, solubility, and purity levels are carefully monitored. Such stringent quality assurance protocols not only confirm the product's suitability for its intended applications but also reinforce trust in its consistent performance.
The production of hydroxyethyl cellulose is a sophisticated process that balances chemical reactions with meticulous purification and quality control measures. Its creation epitomizes the marriage between natural raw materials and advanced chemical engineering, resulting in a product that serves a broad spectrum of industrial needs. From enhancing the texture of lotions to improving the stability of concrete, hydroxyethyl cellulose continues to exemplify adaptability and efficiency, underscoring its role as a cornerstone material in various commercial sectors.