Navigating the Nuances of HPMC Types
In the realm of pharmaceutical manufacturing, the role of Hydroxypropyl Methylcellulose (HPMC) cannot be overstated. This versatile polymer serves as a critical component in a range of formulations, from tablets to capsules and even topical applications. Its popularity stems from its ability to act as a binder, thickener, and disintegrant, among other functions. However, understanding the nuances between different types of HPMC is crucial for optimizing its performance in various formulations.
The first distinction among HPMC types lies in their substitution pattern. The ratio of hydroxypropyl (HP) to methyl (M) groups varies, affecting solubility and gel strength. Low-viscosity HPMC, with a higher proportion of HP groups, tends to be more soluble and is often used for immediate-release formulations. In contrast, high-viscosity HPMC, rich in M groups, provides a stronger gel network, making it suitable for extended-release applications.
Further complexity arises from the differentiation of HPMC based on its viscosity grade. The viscosity grade indicates the thickening power of an HPMC solution and is typically measured in centipoise (cP). Low-viscosity grades (10-100 cP) are ideal for wet granulation processes due to their enhanced solubility. Medium-viscosity grades (3000-6500 cP) find use in sustained-release matrices, while high-viscosity grades (over 10,000 cP) are employed for thickening and stabilizing suspensions Medium-viscosity grades (3000-6500 cP) find use in sustained-release matrices, while high-viscosity grades (over 10,000 cP) are employed for thickening and stabilizing suspensions
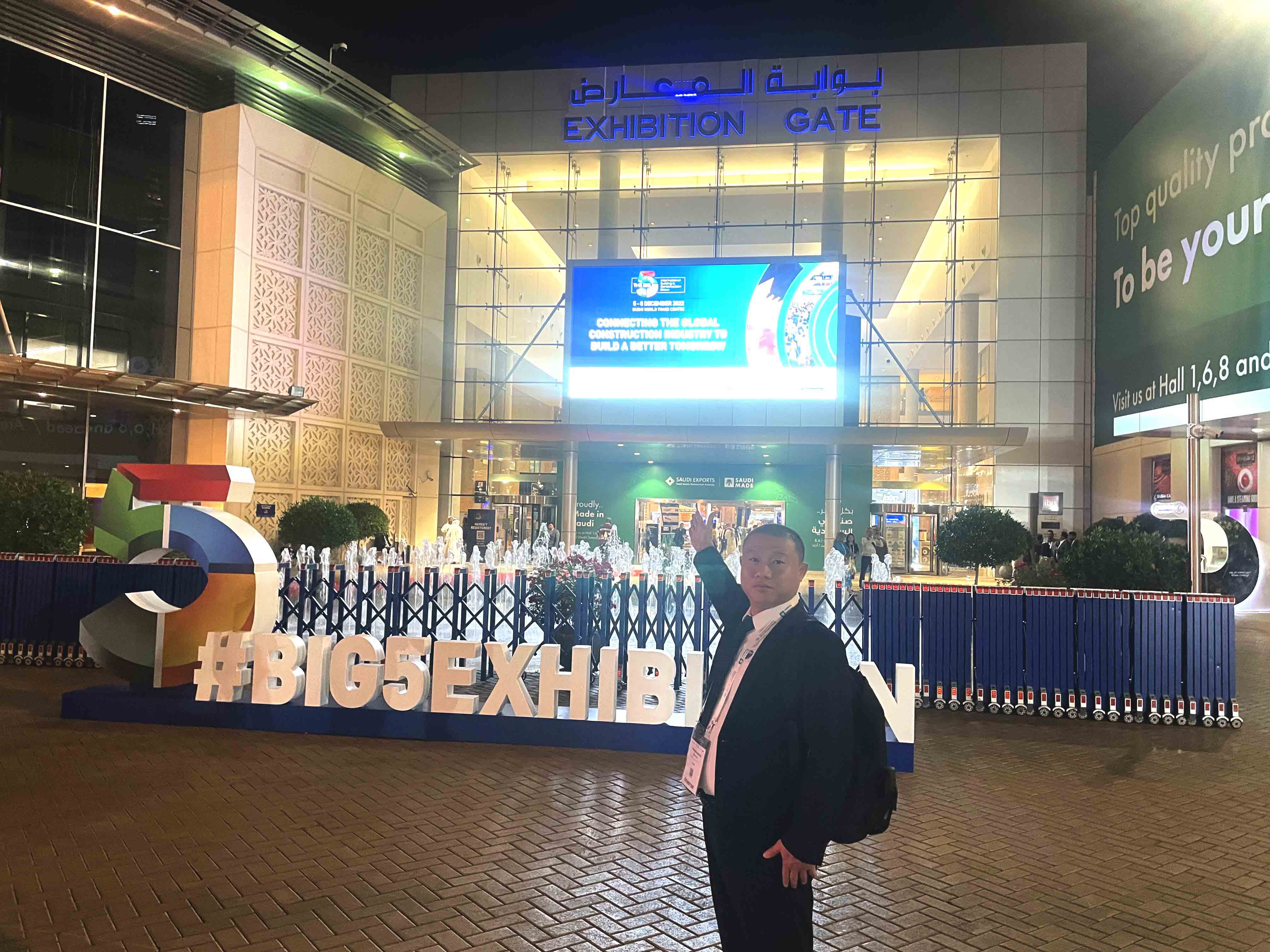
Medium-viscosity grades (3000-6500 cP) find use in sustained-release matrices, while high-viscosity grades (over 10,000 cP) are employed for thickening and stabilizing suspensions Medium-viscosity grades (3000-6500 cP) find use in sustained-release matrices, while high-viscosity grades (over 10,000 cP) are employed for thickening and stabilizing suspensions
hpmc types.
Moreover, HPMC comes in different mesh sizes, which affect its flow properties and blend uniformity during manufacturing. Fine mesh sizes offer better dispersion but may require careful handling to prevent dust formation. Coarse mesh sizes facilitate easier handling but might necessitate adjustments in mixing times to ensure homogeneity.
In addition to these physical attributes, the production process of HPMC can also influence its functionality. Some HPMC types are designed specifically for hot-melt extrusion or direct compression techniques, possessing modified thermal properties that cater to the demands of such processes.
Selecting the right HPMC type is therefore akin to choosing the perfect key for a complex lock. Formulation scientists must consider the target release profile, the manufacturing method, and the desired consistency of the final product. A deep understanding of the molecular structure and physical attributes of HPMC types enables them to fine-tune formulations, ensuring efficacy, safety, and patient convenience.
In conclusion, while HPMC's versatility makes it an indispensable ingredient in pharmaceutical formulations, mastering its variations is essential for achieving optimal product performance. By paying close attention to substitution patterns, viscosity grades, mesh sizes, and production methods, scientists can navigate the subtle yet significant differences between HPMC types, unlocking their full potential in innovative and effective medicines.