HPMC - Hydroxypropyl Methyl Cellulose An In-Depth Look at the Manufacturing Process
Hydroxypropyl Methyl Cellulose (HPMC), a versatile and widely used cellulose derivative, is an essential ingredient in various industries, including construction, pharmaceuticals, and food. It is derived from natural cellulose, a complex carbohydrate found abundantly in plant cell walls. This article delves into the manufacturing process of HPMC, focusing on the hydroxypropyl methyl cellulose factory operations.
The production of HPMC begins with the sourcing of high-quality cellulose, typically from cotton linters or wood pulp. These raw materials are chosen for their high cellulose content, ensuring a pure and efficient end product. The cellulose is then subjected to a series of chemical treatments to create the desired HPMC structure.
The first step in the factory process is the alkalization stage. The raw cellulose is mixed with strong alkali, such as sodium hydroxide, under controlled conditions. This treatment breaks down the hydrogen bonds within the cellulose, making it more accessible for further reactions. The alkali concentration, temperature, and reaction time are critical parameters that influence the final properties of HPMC.
Following alkalization, the modified cellulose is reacted with a propylene oxide (CH3CH2O) solution. This is the key step where hydroxypropylation takes place, introducing hydroxypropyl groups (-OCH2CH(OH)CH3) onto the cellulose backbone. This reaction enhances the solubility and stability of the resulting HPMC in water This reaction enhances the solubility and stability of the resulting HPMC in water
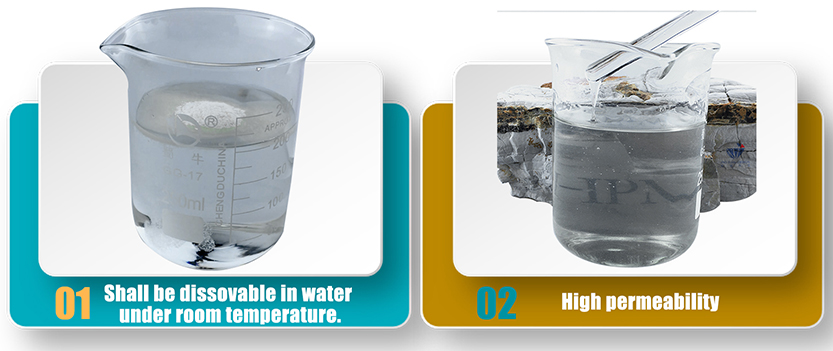
This reaction enhances the solubility and stability of the resulting HPMC in water This reaction enhances the solubility and stability of the resulting HPMC in water
hpmc-hydroxypropyl methyl cellulose factory. The amount of propylene oxide used determines the degree of substitution, which affects the viscosity and other physical properties of the final product.
Subsequently, the hydroxypropylated cellulose is neutralized using an acid, usually acetic acid, to remove any residual alkali. This step ensures the product's neutrality, crucial for its compatibility with different applications.
The final step involves drying and milling the HPMC to obtain a free-flowing powder. The dried material is ground to the desired particle size, which can be tailored according to specific industrial requirements. Quality control tests are conducted throughout the process to ensure consistency and adherence to industry standards.
In a hydroxypropyl methyl cellulose factory, safety measures are paramount due to the handling of chemicals and potential hazards. Strict environmental protocols are followed to minimize waste and ensure sustainable production practices.
In conclusion, the manufacturing process of HPMC in a hydroxypropyl methyl cellulose factory is a complex and precise operation, involving multiple chemical reactions and quality checks. The end product, HPMC, is a testament to the marriage of science and nature, offering a range of benefits across diverse industries. Its versatility, stability, and biodegradability make HPMC a highly sought-after material in today's world.