The Role of HPMC in Enhancing the Performance of Gypsum Plaster
Gypsum plaster, a widely used material in construction and sculpture, is valued for its easy workability, fast setting time, and excellent fire resistance. However, traditional gypsum plaster often encounters issues such as cracking, poor water resistance, and reduced adhesion over time. To address these challenges, the inclusion of Hydroxypropyl Methylcellulose (HPMC) has proven to be a game-changer, significantly improving the properties and performance of gypsum plaster.
HPMC is a type of cellulose ether that acts as a water-soluble polymer, enhancing the flexibility and bonding strength of various materials. In the context of gypsum plaster, HPMC plays a crucial role in several ways. Firstly, it improves the consistency and workability of the plaster mix, allowing for smoother application and a more uniform finish. This is particularly beneficial for intricate designs or large surface areas where consistent application is essential.
Secondly, HPMC enhances the water retention of gypsum plaster. By slowing down the rate at which water evaporates from the mix, it ensures that the chemical reaction between gypsum and water can proceed more effectively. This results in a more complete hydration process, leading to stronger and harder final set products. Additionally, this increased water retention reduces the risk of premature drying and associated cracking, which can compromise the structural integrity and aesthetic appeal of the plasterwork.
Moreover, HPMC imparts improved adhesion to the gypsum plaster
Moreover, HPMC imparts improved adhesion to the gypsum plaster
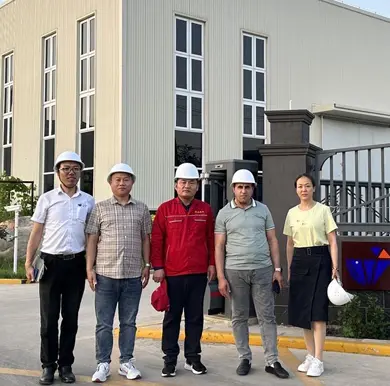
Moreover, HPMC imparts improved adhesion to the gypsum plaster
Moreover, HPMC imparts improved adhesion to the gypsum plaster
hpmc for gypsum plaster. It allows the plaster to form a stronger bond with various substrates, including brick, wood, and concrete. This enhanced adhesion prevents delamination and prolongs the lifespan of the plaster by resisting the forces that could lead to peeling or flaking over time.
The inclusion of HPMC also offers benefits in terms of water resistance. By modifying the way water interacts with the plaster, HPMC helps to create a more hydrophobic surface that resists water penetration. This is particularly useful in damp environments or when the plaster may come into contact with water, reducing the chances of damage and mold growth.
Finally, the use of HPMC in gypsum plaster contributes to an overall greener construction process. As a non-toxic additive that can potentially reduce the need for additional materials or repairs due to its protective qualities, it supports sustainability efforts by minimizing waste and extending the longevity of building components.
In conclusion, the integration of HPMC into gypsum plaster formulations addresses many of the material's inherent limitations. By enhancing workability, water retention, adhesion, water resistance, and contributing to more sustainable building practices, HPMC elevates the performance of gypsum plaster. These improvements ensure that gypsum plaster remains a preferred choice for builders, sculptors, and designers who demand both excellence in performance and aesthetics in their work.